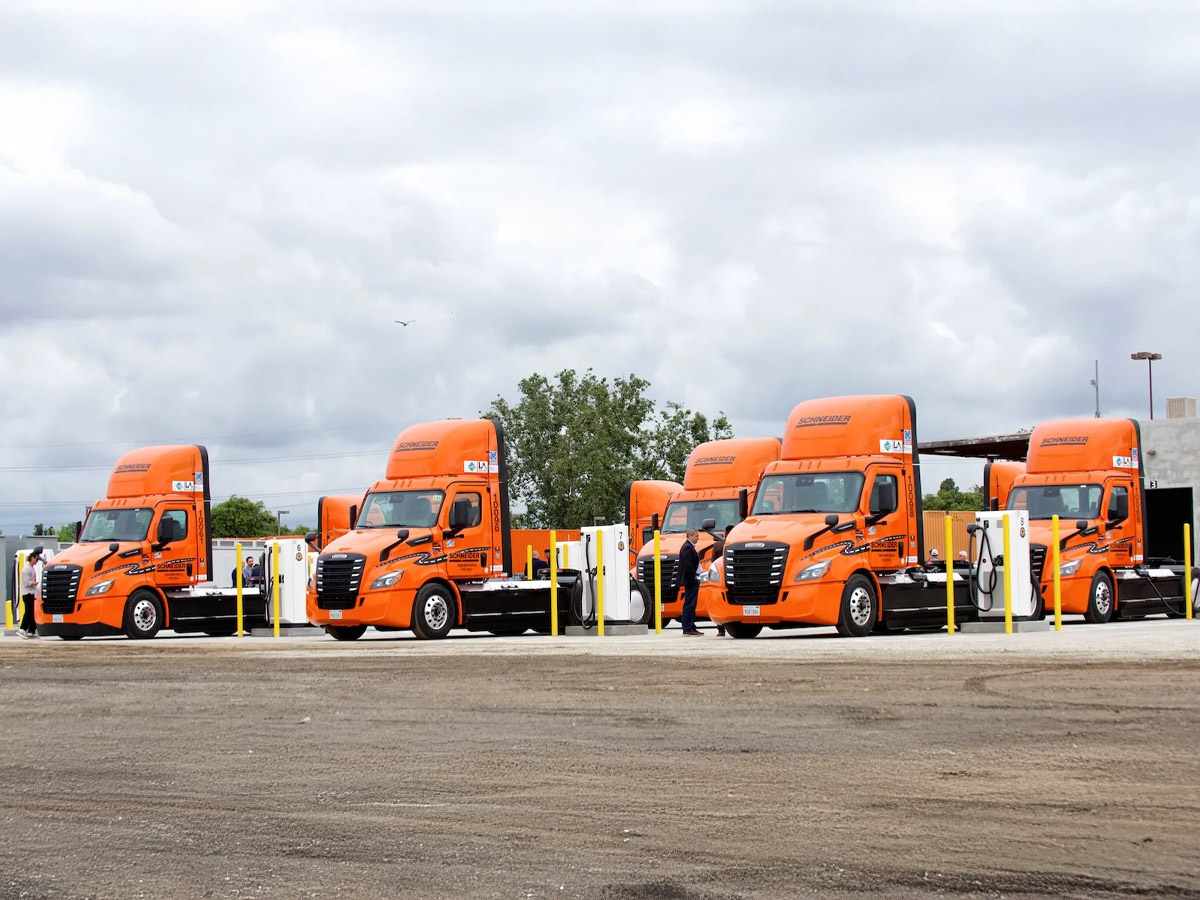
Effective fleet maintenance tips are key to running your fleet efficiently and getting the most out of your vehicles while maximizing uptime. Regular inspections, routine servicing, and staying on top of small repairs can prevent costly breakdowns and extend the lifespan of your fleet.
By prioritizing tire pressure, oil changes and brake systems, you can help keep your fleet safe, reliable and ready to hit the road. Using maintenance scheduling software or even just well-kept files can make the process much easier and keep you on track.
Implementing environmental best practices, such as lowering unnecessary idling time and ensuring proper engine maintenance, further protects your bottom line while making your fleet greener. Armed with these strategies, keeping an eye on your fleet is easier, more efficient, and less expensive.
In this ultimate guide, we’ll cover the best tips to help you practice effective fleet maintenance and avoid damaging downtime.
Key Takeaways
-
Fleet maintenance is essential for maximizing vehicle performance, longevity, and safety. Preventive maintenance A systematic approach with preventive measures and regular inspections is vital to ensure operational efficiency.
-
Proactive fleet maintenance reduces the chance of sudden repairs, resulting in lower operating costs, more reliable vehicles, and safer drivers.
-
Preventative maintenance strategies, such as tailored schedules and routine servicing, help identify and resolve issues early, saving costs on major repairs and reducing service delays.
-
Utilizing tools such as telematics and fleet management software centralizes maintenance monitoring, schedule organization, and documentation for better-informed decisions.
-
Consistent driver and maintenance staff training increases safety, compliance, and operational performance to the agency’s benefit. Foster collaboration across teams and departments to improve communication and proactively report potential problems before they arise.
-
Tracking maintenance metrics—like maintenance compliance rates and repair frequency—guarantees ongoing improvement, thousands of dollars saved annually, and better fleet performance overall.
What is Fleet Maintenance?
Fleet maintenance is a proactive, systematic approach to vehicle lifecycle management that ensures productive vehicles are always in peak working condition. It integrates routine inspections, immediate repairs, and preventative actions to deliver best-in-class safety and reliability. This process is more than just being proactive about problems.
It gets to the heart of proactively identifying and resolving potential brand or operational problems before they become disruptive. When implemented correctly, fleet maintenance protects businesses from preventable expensive downtime and loss of efficient day-to-day operations.
If you think of a full-scale fleet maintenance program, it’s the oil changes, it’s the checking and replacing of filters, and doing tire rotations and aligning the systems. This complementary series of routine activities makes it possible for every vehicle to maximize operations and maintain safety requirements.
As an example, quarterly overhauls offer a comprehensive look at key components such as suspension systems, brakes and transmissions. Regular inspections and preventive maintenance ensure these vehicles are in top shape for the long haul, preventing unplanned vehicle breakdowns.
Tracking fuel purchases and monitoring vehicle use are both valuable, but basic, yardstick duties. They help you discover new ways to increase fuel efficiency, thereby cutting your fuel costs. In reality, 55% of fleet managers surveyed achieved fuel cost savings of at least 10% by following these practices in a consistent manner.
Safety is top priority in fleet maintenance. Prevention regular inspections, part of drivers’ daily pretrip routine, can identify small problems before they become serious hazards. Having these inspections records on hand makes sure everyone is accountable and helps spot trends, which can increase operational efficiencies even more.
Preventive maintenance extends the lifespan of the fleet’s vehicles, reducing taxpayer burden by lowering replacement costs in the long run. Armed with connected management solutions, businesses can proactively schedule maintenance to avoid downtime, monitor performance across all assets, and make decisions based on real-time data.
Why Fleet Maintenance Matters
Fleet maintenance is the unsung hero behind any smooth-running operation—keeping your vehicles out on the road, reducing costly downtime, and maintaining healthy profit margins.
Improving Business Productivity
A well-maintained fleet undoubtedly produces a positive, direct impact on your business’s productivity through improving vehicle reliability, lessening breakdowns, and extending asset life. When vehicles are always available and working at peak performance, they lead to more efficient workflows and improved customer experience.
Driver Safety First
Regular maintenance is essential to protect drivers and passengers. For example, a fleet’s routine inspections can identify a burned-out brake or damaged tire before they become hazards that lead to an accident.
Beyond the technology of gas and electric vehicles, essential advanced safety features like automatic braking systems or lane assist help keep drivers safer. Drivers are the first line of defense behind the wheel. They need to be the first line of defense in flagging any excessive noise, vibration, or dashboard indicator light ASAP.
Provide training to ensure your team understands that safety comes first and that communication is always welcome. Taking this approach will reduce liability and foster a safer working environment.
Lower Operating Costs
Preventative maintenance is one of the most well-known and cost-effective practices to save money. Tackling small troubles in advance, like changing out filters or taking care of engine deterioration, prevents expensive fixes down the line.
Keeping tires properly inflated and engines regularly tuned are common practices that save fuel. One of fleet managers’ top priorities is tracking maintenance costs through thorough maintenance logs.
You can identify major recurring issues and reduce spending on repair costs, ensuring you’re running a financially sound operation.
Minimize Service Delays
Better yet, a proactive maintenance schedule stops disruption in its tracks, dealing with problems before they can cause downtime. Fleet management software makes it easy to schedule maintenance, track a vehicle’s entire service history, and perform timely interventions.
Coordinating with drivers about maintenance needs keeps vehicles available for critical tasks, maximizing revenue.
Maintain Legal Compliance
Adhering to legal standards requires keeping current with all management regulations, including regular vehicle safety inspections and driver duty time regulations.
Keeping thorough and accurate fleet maintenance records provides proof of compliance during audit inspections, shielding your business from nasty fines.
Types of Fleet Maintenance
Effective fleet management relies on understanding the two main maintenance approaches: preventative and reactive. Each plays an invaluable part in guaranteeing vehicles stay safe, productive, and affordable throughout their life-cycle. By striking the right balance between these two approaches, you’ll be able to keep your fleet performing effectively, while avoiding excessive downtime or unplanned costs.
Preventative Maintenance Approach
Preventative maintenance is designed to prevent large, expensive breakdowns by fixing smaller issues before they develop. This means developing a calendar specific to each vehicle, with services triggered by either mileage accumulated or elapsed time since the last service. Monthly checks include all required maintenance such as oil change, tyre rotation and tune up plus complete safety checks.
By comparison, quarterly overhauls go further with penetrating inspections to the suspension and transmission systems. Preventive maintenance inspections are the best way to identify potential issues before someone wears down their tires or their brakes. Drivers can contribute by performing daily checks on tires, oil levels, and safety components, reporting concerns promptly.
This is where fleet management software really comes in handy, automating reminders for scheduled maintenance such as filter replacements or diagnostics. Consistent staff training helps keep these routines a priority, helping maintain a level of consistency that prevents long-term repair costs down the line.
Reactive Maintenance Approach
Reactive maintenance deals with unanticipated problems such as fleet breakdowns or accidents. Though needed, it conditions more often than not comes at an increased cost and stalls fleet operations. For example, an unexpected transmission fix may ground a vehicle temporarily, lowering the fleet’s Utilization Percentage.
To overcome these obstacles, have a go-to plan for dealing with unplanned repairs, from immediate access to service centers to spare vehicles and more. Transforming the culture to value proactivity over-reactivity minimizes dependency on inefficient reactive approaches. A balanced approach ensures preparedness while prioritizing preventive strategies for long-term success.
How to Maintain Your Fleet?
Keeping your fleet in tip-top shape starts with an all-inclusive plan that helps keep every vehicle safe, efficient and reliable. Traditional preventative maintenance is solely focused on mileage and service date. It prevents expensive downtime and catastrophic damage that would put vehicles out-of-service for weeks.
Given that annual maintenance costs can easily be in the tens of thousands of dollars per vehicle, a strategic and thoughtful approach is needed.
1. Select Suitable Vehicles
Selecting vehicles that are purpose-built to meet your unique business requirements provides a solid foundation for smart fleet maintenance. Look beyond just load capacity, fuel efficiency, and other basic reliability metrics.
For instance, a delivery fleet might focus on fuel-efficient vans, but construction firms will require heavy-duty trucks. When choosing vehicles, aligning vehicle selection with your maintenance goals will save money and keep operations efficient in the long run.
2. Create Vehicle-Specific Plans
Whether electric or traditional, each vehicle in your fleet has specific needs. Monitor fleet telematics data to determine when you should perform maintenance, so you’re not wasting resources on unnecessary checks and repairs.
By documenting each vehicle’s maintenance history, you will be able to better hone these plans and quickly adjust to any changes in vehicle performance or operational needs.
3. Use Maintenance Metrics
Metrics such as Downtime Percentage or average repair cost help give you clear, actionable insight into how your fleet is performing. For example, a rising Downtime Percentage is an indicator that you need to start doing more proactive maintenance.
Sharing these metrics and success criteria with your team fosters accountability and a culture of continuous improvement.
4. Train Drivers on Tire Checks
Drivers are essential to fleet maintenance. Fleets don’t do maintenance in vacuums. Daily tire inspections, using a consistent checklist, catch problems before they become dangerous, such as excessive wear or puncturing.
Encouraging prompt reporting of safety-related concerns helps to ensure quick resolutions, protecting vehicle safety.
Proactive Maintenance Strategies
Keeping a fleet proactive with maintenance is key to reducing fleet downtime, improving the lifecycles of vehicles, and ensuring they meet safety and environmental regulations. By integrating structured approaches like regular inspections, predictive analytics, and telematics solutions, you can ensure a healthier, more efficient fleet.
Reduce Fleet Downtime
Vehicle downtime is minimized when vehicle maintenance is planned during off-peak operations (energy being used while the vehicle is not in use). For instance, regular maintenance can be performed on weekends or after hours. This flexibility should be customized based on your specific business operations.
Preventative measures are crucial—monitor repair turnaround times. It’s equally important to monitor repair turnaround times. Tracking delays can help illuminate areas where service workflows are bottlenecking. Measuring the impact of downtime on productivity helps you make better schedule changes or resource assignments.
Integrate Predictive Analytics
Predictive maintenance in particular is a revolutionary strategy. By taking advantage of historical data and failure trends, you’re able to predict potential problems before they become major issues. According to one study, companies that have adopted predictive analytics have lowered their repair costs by more than 60%.
Technologies such as PDMs monitor the real-time health of equipment, maximizing the usable lifespan of the vehicle and improving overall availability. By training your team on predictive analytics, you can allow them to make better decisions and maximize the use of valuable resources.
Optimize Fleet Health with Telematics
Telematics systems give fleets 24/7 access to vehicle performance data. Alerts for urgent concerns, like engine failures, allow for immediate action, and data accumulated helps with more efficient service timing.
For instance, Taabi’s telematics solutions have allowed their clients save on fuel costs and prolong vehicle life. A data-driven approach ensures informed maintenance planning and long-term savings.
Improve Record-Keeping with Software
Digital fleet management software helps to centralize all maintenance data, making it both more efficient and easily accessible. Tracking service history, costs, and compliance helps identify trends and plan future servicing.
For instance, scheduling quarterly overhauls for suspension or transmission systems complements monthly oil changes and tire rotations, keeping fleets in top condition.
Key Performance Indicators (KPIs)
Key Performance Indicators (KPIs) are essential to manage and optimize maintenance efficiency of the fleet. Focus on quantifiable metrics to determine progress and optimize processes. By taking this approach, you’ll be able to make better, more informed decisions that save costs and keep your vehicles healthy.
Read on as we dive into key KPIs to improve your fleet management approach.
Assess Maintenance Efficiency
The journey to evaluate maintenance efficiency properly starts with analyzing some key performance indicators (KPIs), including maintenance compliance percentage, average repair costs, and other related metrics. This results in increased breakdown risk, although high compliance rates, like the industry-standard 95% Preventative Maintenance Compliance, guarantee timely and regular servicing.
Regularly reviewing maintenance schedules and processes can uncover inefficiencies, like delays or redundant steps, allowing for targeted adjustments to improve performance.
Track Asset Utilization Rate
Measuring how well assets are being utilized can ensure your asset-heavy fleet is being as productive as possible. For example, unnecessary underutilized vehicles elevate the fleet’s Total Cost of Ownership (TCO).
Monitoring this KPI can help inform the size and distribution of your fleet. Beyond immediate outcomes, data trends on utilization can help anticipate future demand, guiding purchasing plans or maintenance cycles, so every fiscal dollar is maximized.
Monitor Preventative Maintenance Frequency
Preventative maintenance frequency has a strong correlation with fleet reliability. Measuring this KPI helps keep your schedules on track, so you’re not blindsided by last-minute repairs.
Implementing software-assisted automated scheduling reminders boosts compliance and fosters a culture of proactive maintenance, avoiding unanticipated and expensive downtimes.
Evaluate Technician Productivity
Technician performance, as measured in various ways like repair times and quality, has a major impact on operational efficiency. Setting clear productivity expectations, consistent monitoring of productivity levels, and continuous employee training can all help close skills gaps.
To take one example, a faster turnaround on repairs at known quality level increases fleet uptime and reduces maintenance costs.
Track Repeat Repairs
First, repeat repairs signal a clear, avoidable problem. By keeping track of these incidents, we can target the root causes, whether that’s a faulty part or procedural error.
Making results public creates an added level of accountability that pushes the team to always improve upon their previous work.
Tailor Maintenance Schedules
According to a recent study, customizing maintenance schedules is critical for maximizing fleet performance while reducing downtime. Learn the maintenance needs unique to each vehicle and sector. This understanding will set you up to build proactive strategies that result in efficient, long-lasting fleets.
Different Vehicle Types
Each vehicle type in your fleet will have different maintenance needs. This is because light-duty vehicles rack up more miles, thus necessitating more oil changes. At the same time, heavy-duty trucks require specialized maintenance for their elements like their braking systems.
Creating customized maintenance schedules for light, medium, and heavy-duty vehicles helps make sure all vehicles receive the proper attention. Performance metrics, like fuel efficiency and repair frequency, need to be tracked and measured to continue improving these schedules.
Tailoring your maintenance schedules and training your maintenance team to understand the specific needs for different vehicle types can save time and increase precision.
Industry-Specific Practices
Every industry has unique maintenance needs driven by the context in which they work. As an example, delivery and service fleets have critical stop-and-go use, but construction vehicles take extreme wear in rugged environments.
Researching industry standards and collaborating with experts helps implement best practices. By regularly reviewing these strategies, fleets can help to ensure they stay in line with the ever-evolving needs of the industry, increasing fleet longevity and reliability.
Communicating Schedules
Well-defined and well-communicated tailored maintenance schedules to both drivers and maintenance staff are just as important. Monitoring inspections via DVIRs and implementing tailored daily vehicle inspection reports helps ensure that everyone is on the same page.
When drivers are empowered to take simple checks and proactively report issues, fleet managers have the information they need to proactively adjust schedules.
Train Maintenance Staff
Properly trained train maintenance personnel is the first step toward successful fleet maintenance. Provide your train maintenance staff with the right tools and knowledge! This will improve performance of the vehicles, increase their longevity and reduce costs.
Modern Vehicle Diagnostics
Recent technology diagnostics are the key to helping accurately diagnose a vehicle’s problems. With new equipment like onboard diagnostic scanners, they can immediately identify any engine or system issue preventing the train from operating, drastically cutting down time spent troubleshooting.
By empowering your staff to leverage these technologies, you provide a path to speedier, more informed repairs. For example, a technician skilled in using diagnostic software can identify fuel system inefficiencies that might otherwise go unnoticed, preventing costly breakdowns.
Routine diagnostic scans are equally important to catch problems early. For example, by running a scan once a month, you will be able to identify small issues, such as battery voltage inconsistencies, before they turn into expensive repairs. Keeping abreast of diagnostics developments, like AI-based technologies, will help make sure your maintenance staff is ready to meet tomorrow’s challenges today.
Stay Updated on Industry Trends
Innovation happens incredibly quickly in the fleet maintenance landscape. Push your maintenance team to subscribe and read industry publications including Fleet Maintenance Magazine to stay up to date with advancements and best practices.
Workshops and conferences provide hands-on exposure to new tools, like advanced tire pressure monitoring systems, that improve safety and efficiency. Valuable peer-to-peer networking, maybe through local chapters of fleet management associations, helps provide community and accountability.
Foster a culture of innovation, internally and externally. This mindset makes your team more receptive to new practices and new technologies such as predictive maintenance systems, improving your operations even further.
Data Analytics for Cost Savings
Using data analytics, the fleet maintenance overhaul revealed new areas to find cost savings that were previously hard to see. Telematics and other smart devices offer quick, easily digestible reports on emissions, fuel consumption, and other metrics tied to vehicle performance.
These technologies are making vehicles themselves data gold mines, enabling fleet managers to identify when vehicles need maintenance, and when they do not, with unprecedented accuracy. Predictive maintenance, driven by IoT sensors, addresses problems before they develop into costly failures.
By catching these issues early on, it avoids expensive repair costs and reduces equipment downtime. In reality, telematics has allowed dependent fleets to save as much as 14% on fuel costs.
Drive Cost-Effective Improvements
By analyzing maintenance records, SKF and BNSF can see patterns and areas of opportunity to improve operations. For example, monitoring the types of repairs needed most frequently could uncover missed opportunities with vendor services provided, or a lack of training among agency staff.
Proactive, cost-effective strategies like combining service schedules or transitioning to longer-lasting replacement parts to reduce service frequency help cut costs where they count without compromising quality. Monitoring the impact of these measures, like reduced downtime or fewer emergency repairs, ensures they contribute positively to fleet performance.
Creating a culture of accountability with maintenance teams drives efficiency and compliance with these strategies.
Measure Key Performance Metrics
Setting metrics such as maintenance compliance rates or average repair costs would be necessary to measure outcomes. Consistently examining data allows agencies to see what trends may be developing, like which vehicles are in constant need of maintenance.
Sharing these insights with your operations and maintenance teams helps to cultivate transparency and create a desire to improve across the team.
Implement Digital Record Keeping
Interoperable digital record-keeping systems allow service histories, costs, and compliance data to be accessed in one central place. By automating odometer tracking and expense management, fleet managers can easily calculate real-time cost-per-mile instantly available, promoting better decisions and future planners.
Regulatory and Safety Considerations
Weaving through these regulatory and safety considerations while maintaining and managing a fleet takes a clear comprehension of industry-specific regulations. It requires something more—a deep commitment to being proactive. These considerations play a critical role in ensuring the safety of drivers and DOT assets, reducing risk of liability exposure, and maintaining compliance with evolving standards.
Influence Fleet Maintenance Practices
Regulatory constraints play an important role in determining fleet maintenance strategies. Industries such as oil and gas operate under the narrowest of strict directives. Specifically, they must zealously adhere to hours-of-service (HOS) regulations and hazardous material disposal guidelines.
Make sure your maintenance practices match these standards. Ensure vehicles comply with existing Department of Transportation (DOT) inspection standards, including ensuring engines, transmissions, and exhaust systems are functioning.
So to be compliant, it’s important to stay on top of constantly evolving regulations. Tools such as AttriX’s Electronic Logbook, certified by Transport Canada and FMCSA, streamline tracking and reporting requirements to make life easier.
Have your fleet staff trained to understand the importance of compliance. Consistent training and regular review will increase their compliance with safety and legal requirements.
Prioritize Safety Over Reaction
Protecting safety must become the dominant value in our maintenance practices. Focusing on preventive measures, like pre-trip inspections and maintenance to avoid malfunctions, keeps everyone safe and saves fleets from expensive repairs.
Proper upkeep of your safety equipment, from fire extinguishers to first aid kits, is just as essential. Fleet managers can increase safety by ensuring their employees are trained on reporting procedures.
They need to use data to track metrics, especially to identify where they need to improve. These annual inspections, both federally mandated and required by many states, counties, and cities, commit to making sure vehicles are safe and fit to drive.
AttriX’s solutions, tailored to Canadian territories, exemplify how fleets can integrate compliance with safety, supported by CFTR-certified experts and practical tools.
Fuel Efficiency and Maintenance
Fuel efficiency is inextricably linked to the overall maintenance of your fleet. Routine maintenance helps vehicles operate effectively while using fuel efficiently. It’s the little things, such as improper tire inflation or a clogged air filter, that really add up to wasted fuel.
Correcting and maintaining these through preventative inspections prevents excess wear and tear on engines, saving agencies in operational costs.
Benefit Overall Fleet Performance
First, smart maintenance practices have a direct impact on fleet performance, as maintenance helps ensure that vehicles stay in the best condition possible. In fact, things like timely oil changes and regular tire rotations improve engine performance and efficiency and prolong tire life.
When performance metrics like kilometers per liter are measured consistently, it is easy to spot vehicles that are underperforming. This information enables you to proactively shift maintenance treatments or schedules based on immediate future needs or prioritize more expensive repairs.
Targeted actions, such as installing fuel-efficient tires, further maximize operations for added fuel efficiency. By communicating this information clearly with your team, you help create a culture of excellence that empowers everyone to play a role in continuous improvement.
Control Fuel Costs
Improving fuel efficiency begins with smart maintenance. Quick routine maintenance—routine inspections or pressure checks on tires, fuel systems, and alignment—helps keep the vehicle running efficiently and regularly.
Tracking trends in fuel consumption can reveal poor practices like idling or carrying too much weight. If these problems are fixed quickly enough, we can save hundreds of liters of fuel each week.
Training drivers in fuel-efficient habits, like maintaining steady speeds and avoiding aggressive acceleration, complements maintenance efforts, creating a comprehensive strategy for cost control.
Additional Fleet Management Tips
Fleet maintenance is more than just regular oil changes and tune ups. Prioritizing these disciplined approaches and teamwork will maximize the safety, performance, longevity of your fleet’s vehicles while maintaining operational efficiency.
Gather Regular Driver Feedback
Drivers are frontline workers when it comes to vehicle performance. Prompting them to provide feedback regarding mechanical problems or performance-related issues keeps maintenance at the forefront and ensures issues are caught before they become critical.
Feedback can be gathered in real time via surveys or with regular check-ins, letting trends start to bubble to the surface. For instance, if several drivers report a problem with braking, you can focus resources on inspecting the brake system.
Open lines of communication create a team atmosphere where your drivers and maintenance team are working together to keep vehicles healthy and safe.
Create Fleet Inspector Role
A dedicated fleet inspector, who sweeps the lot every day, proposes a robust culture of inspection and compliance. This job description includes tracking vehicles’ maintenance schedules, performing regular inspections, and making sure vehicles are safe.
For example, an inspector may run weekly checks on tire pressure and tread to prevent damage from wear. By working a little more closely with the maintenance team, the inspector is able to drive where repairs and servicing are getting done right or dropped in queue.
Keep Vehicles Clean
Routine washing maintenance washes away dirt and grime damaging paint and metal and staving off corrosion while keeping fleets looking great. Dust build-up can clog air filters, and road grime can cause rust.
A regular overhead cleaning schedule, paired with the right techniques, will prevent damage during the process. An example would be to use non-abrasive cleaners for windshields, which can improve visibility and safety.
Clean vehicles feel better and drivers take greater pride knowing they’re helping to improve air quality, contributing to a boost in employee morale.
Implement Driver Checklists
Equipping drivers with uniform pre-trip inspection checklists can help create organization and consistency. These checklists could include things like tire wear, fluid levels, and lighting.
Having drivers trained to fill out these checklists creates a sense of accountability. Additionally, having them continually updated will make sure they cover new, developing maintenance needs.
Conclusion
Smart fleet maintenance ensures your fleet will continue to operate safely and efficiently while saving you money and providing uninterrupted service. Attending to maintenance proactively is not only more efficient, it inspires confidence in your drivers and helps keep safety a top concern. Measuring what matters and being data-driven enables you to plan more strategically and save money. Proper planning and an educated, properly equipped staff go a long way in maintaining vehicles reliably enough to ensure they are always ready when it’s time to roll.
Simple measures, such as keeping an eye on tire pressure or tracking fuel consumption go a long way over time. Every step goes a long way in maximizing your fleet’s longevity and minimizing nasty surprises. When you concentrate on the most effective strategies, you’ll be able to maintain a lower cost and higher performance. Take these tips and apply them today—get a firsthand experience as to how this will positively impact your fleet and your bottom line.
Frequently Asked Questions
What is fleet maintenance?
Fleet maintenance refers to the process of regular inspection, repair, and servicing of vehicles and equipment used in a fleet. It means preventive care like oil changes, tire rotation and replacement, engine diagnostics and more. With proper fleet maintenance, you will experience fewer breakdowns, increase your vehicle’s lifespan, and make your fleet safer.
Why is proactive fleet maintenance important?
Effective proactive fleet maintenance prevents unexpected breakdowns, reduces repair costs, and keeps your fleet safe. Most importantly, it allows you to mitigate issues at an early stage, keeping vehicles on the road and extending fleet uptime.
How can data analytics improve fleet maintenance?
Data analytics monitors overall vehicle performance, spots emerging trends, and predicts what could go wrong with specific units. This enables scheduling optimization, cost reduction, and improved operational decision making to increase fleet efficiency.
What are key performance indicators (KPIs) for fleet maintenance?
Some of the key fleet maintenance KPIs are vehicle uptime, fuel efficiency, maintenance costs and repair turnaround time. Keeping track of these is the best way to know how you are performing and where you need to improve.
How does fleet maintenance affect fuel efficiency?
Clearly, well-maintained vehicles are safer, more convenient, save money on fuel and emissions. Regular checks like tire pressure and engine tuning improve fuel efficiency and save costs.
What should be included in a fleet maintenance schedule?
This is where a fleet maintenance schedule comes in – the regular vehicle inspections, oil changes, tire rotations, brake checks, anything and everything. Adjusting it to the specific manufacturer recommendations is important to ensure the best performance.
Why is staff training essential for fleet maintenance?
Having trained staff on hand leads to better vehicle maintenance outcomes, faster identification of issues, and more efficient repair turnaround times. This reduces downtime through more proactive maintenance, mitigates safety risk, and improves fleet reliability.